- Safety Knights Monday Mailer
- Posts
- New Post
New Post
THIS WEEK’S TIPS
This week’s safety upgrades:
ASSP Conference News
Selling Safety to Upper Management
New Health and Safety Research
PROFESSIONAL DEVELOPMENT
This Weeks Professional Development Tip
SAFETY KNIGHTS COMMUNITY
We Need to Hear From You.
Do you like potentially winning money?

Well, come fill out our survey to be entered to win one of four $25 Amazon Gift Cards. And, help us make Safety Utopia!
Link here: https://lnkd.in/g33svWag
SAFETY MANAGEMENT
Speak Your CEO’s Love Language
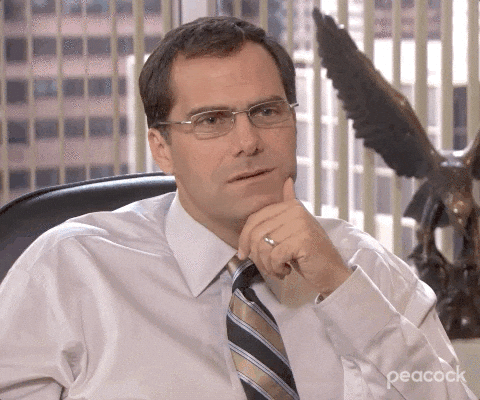
In many organizations, safety is often viewed as a basic compliance requirement rather than a key driver of business performance. Companies invest significant resources into ensuring safe products and workplaces, largely motivated by regulatory demands and the need to avoid legal liabilities. Despite these efforts, safety issues continue to plague industries, leading to frequent product recalls and workplace accidents. This approach often stems from a fundamental misunderstanding of safety's potential as a strategic asset. By shifting the focus from mere compliance to proactive safety management, companies can not only reduce risks but also enhance their overall business performance, driving customer satisfaction, employee well-being, and long-term profitability.
Reframing Safety as a Performance Driver: a five-step process for turning safety into a competitive advantage:
Align on Meaning: Companies need to define what safety means for their organization clearly. This alignment ensures that everyone, from top management to frontline employees, understands the importance of safety and how it contributes to the company’s goals. An example is Alcoa, where former CEO Paul O’Neill made zero workplace injuries a central part of the company’s strategy.
Agree on Metrics: It’s crucial to link safety metrics to business outcomes. Instead of tracking numerous unrelated safety metrics, companies should focus on a few key indicators that directly correlate with performance improvements. For example, a Pennsylvania nursing-home system linked safety metrics like fall rates to resident retention and business growth.
Anticipate and Prevent Problems: Companies should adopt practices that anticipate and prevent safety issues before they occur. This proactive approach can involve using technology to monitor safety, training employees to recognize potential hazards, and implementing systems to address risks before they materialize.
Targeted Training: Safety training should be specific, relevant, and convenient for employees. Generic safety training is often ineffective, so companies should focus on training that directly correlates with improved safety outcomes. For example, targeted training in bedsore prevention at a nursing-home chain led to significant safety improvements.
Incentivize Employees: Companies should incentivize behaviors that lead to safe outcomes, rather than just rewarding the outcomes themselves. This approach encourages proactive safety practices among employees and helps embed safety into the organizational culture.
3motionAI
Your Ergo Solution.
Overexertion is costing companies $12.49 BILLION each year and feeding into a much larger problem! That’s why we’ve partnered with 3motionAI to enhance workplace safety with their Risk Flashlight solution. Together, we’re empowering EHS professionals to tackle these costly problems at the root, building a safer, more equitable workplace.
Steps to Take:
1. Learn more about 3motionAI: Read, here
2. Show company leadership how you can protect the bottom line.
3. Earn the respect you deserve by making a real impact.
CONSTRUCTION
Largest Construction Contractor Studying Heat.

Turner Construction, the largest U.S. contractor by revenue is actively addressing heat-related health issues among construction workers through a comprehensive study focused on the effects of high temperatures. This month, the company will monitor 200 workers in the Midwest, significantly expanding on last summer’s pilot project, which involved a smaller group of 33 workers over three days. The study aims to gather extensive data on how heat impacts workers’ health and to identify effective heat mitigation strategies that can inform future health initiatives on job sites. In the pilot study, workers ingested a pill-sized device that continuously monitored their internal body temperatures for 24 hours, providing valuable real-time insights into the effects of heat.
Findings from the pilot highlighted the critical importance of hydration, showing that workers should hydrate both in the morning and throughout the day, regardless of temperature or activity level. The current research involves collaboration among various organizations, including Turner Construction’s foundation, Flatiron Construction, insurance companies Liberty Mutual and Chubb, and health research nonprofit La Isla Network. Turner has also integrated specific heat safety plans into every contract and project, which include establishing hydration stations and shaded areas for workers to cool off.
Innovatively, the company has employed strategies such as using a urine color chart in jobsite restrooms to help workers visually monitor their hydration levels. As the current study progresses, Turner anticipates generating more detailed recommendations for combating heat-related health risks, ultimately contributing to a safer working environment for construction workers and setting best practices for the industry.
WORKPLACE SAFETY
Are The Kids OK?
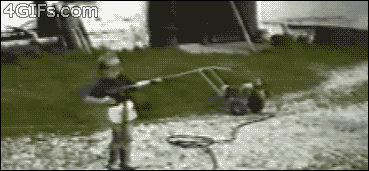
Recent studies indicate that young workers (aged 15–24 years) in the United States experience significantly higher rates of job-related injuries compared to adults. Data from the National Electronic Injury Surveillance System (NEISS-work) from 2012 to 2018 show that young workers have annual rates of emergency department-treated injuries that are 1.2 to 2.3 times higher than those for adults aged 25–44, with the highest rates found among workers aged 18–19 years. The lack of adequate job training and safety skills has been identified as a major contributor to these injury rates, with many young workers reporting that workplace safety training is either nonexistent or ineffective.
Historically, a significant percentage of teens have participated in summer employment, with about 36.6% of U.S. teens having jobs in the summer of 2021. While work can promote healthy youth development and teach essential skills, most young people enter the workforce unprepared for safety and health risks. Interviews with school administrators revealed that only one-third of school districts provide substantial workplace safety and health instruction.
To combat this issue, the National Institute for Occupational Safety and Health (NIOSH) and the American Industrial Hygiene Association (AIHA) developed the Safety Matters program. This one-hour interactive educational module aims to raise awareness about workplace safety and health, equipping young people with the skills needed to actively participate in creating safe work environments. The program is designed for youth in grades 7 through 12 and includes an instructor’s guide, PowerPoint presentation, and short videos, all available for free on the NIOSH and AIHA websites.
Safety Matters is based on the Youth@Work—Talking Safety curriculum, which has been shown to significantly improve safety knowledge and attitudes among students. The program offers a concise introduction to workplace safety, making it accessible for schools and organizations that cannot commit to longer training sessions. Although research on the effectiveness of one-hour health promotion programs is limited, preliminary studies suggest that brief educational interventions can lead to significant knowledge and attitude changes.
The pilot project assessing the Safety Matters program in Colorado found statistically significant increases in both workplace safety knowledge and attitudes among participants, demonstrating its potential as a valuable resource for improving safety awareness among young workers. Overall, Safety Matters presents a promising, community-based approach to providing essential workplace safety education, setting a foundation for further job-specific safety training.
OSHA/ASSP
OSHA's Strategic Safety Initiatives: Key Updates from the ASSP 2024 Conference

Last week at the American Society of Safety Professionals (ASSP) Safety 2024 conference, Douglas Parker, Assistant Secretary of Labor for Occupational Safety and Health, shared OSHA's latest initiatives aimed at enhancing worker safety across various industries. From modernizing longstanding programs like the Voluntary Protection Programs (VPP) to addressing urgent safety concerns through new rulemaking efforts, OSHA is taking a collaborative and proactive approach. This article delves into the key updates and ongoing efforts discussed during the conference, highlighting OSHA's commitment to creating safer workplaces for all.
VPP Modernization
Modernization Efforts: OSHA aims to improve its Voluntary Protection Programs (VPP) by making them more accessible and effective. The plan involves creating different levels within the program to incentivize participation, starting with low barriers to entry and progressing to more robust requirements.
Safe + Sound Week: OSHA's Safe + Sound Week focuses on job hazard analysis (JHA) to identify hazards before they occur, aiming to triple participation from last year.
Current Focus Areas
National Emphasis Programs (NEP): OSHA is targeting high-hazard industries and vulnerable workers. Key NEPs include fall prevention and warehousing, which address significant injury rates and specific hazards like material handling and heat.
Fall Prevention: A major focus due to the high number of fatalities related to falls, especially in construction.
Warehousing Emphasis: This sector has seen significant growth, with injury rates higher than the private sector overall.
Rulemaking Efforts
Heat Safety: OSHA has proposed a new rule to protect workers from heat-related hazards, though it is still under review. The rule is modeled after successful state programs.
Infectious Disease Standard: Progress is being made on a standard for healthcare, with plans to address workplace violence prevention next.
Worker Walkaround Rule: OSHA is developing a rule to allow employees to designate a representative during inspections.
Broader Initiatives
Corporatewide Issues: OSHA is focusing on corporatewide safety issues, with tools like the Severe Violator Enforcement Program (SVEP) to address high-hazard employers across any industry.
National Settlements: OSHA has reached settlements with companies like Dollar General and Dollar Tree to ensure significant safety investments and improvements.
Aggressive Enforcement: For repeat offenders, OSHA is taking more aggressive actions, including prosecutions, to ensure hazard abatement, with a notable success in reducing trenching deaths by 50%.
Empower Your Teams With Positive Accountability
Jessica Kriegel, Ed.D., Chief Scientist of Workplace Culture at Culture Partners, addressed the challenge of fostering a culture of accountability in organizations. In her keynote, "Empower Your Teams With Positive Accountability," Kriegel highlighted that accountability is often "weaponized," seen as placing blame rather than driving results. She introduced the "Results Pyramid" model, emphasizing that lasting cultural change requires addressing not just actions but also the underlying beliefs and experiences that shape accountability. By shifting focus from merely implementing strategies to cultivating the right beliefs through impactful experiences, organizations can achieve more meaningful and sustained improvements in their safety culture.
Closing Key Note - Embrace Creativity & Innovation
Kyle Scheele delivered a keynote address titled "Thinking Inside the Box: How Tough Times Fuel True Creativity & Innovation." In his speech, Scheele discussed how challenges and constraints, such as limited resources, can actually foster creativity and drive innovative solutions in workplace safety. He highlighted examples like the Apollo 13 mission, where engineers creatively adapted to severe limitations, to demonstrate how obstacles can be turned into opportunities for improvement.
Scheele also provided practical advice for overcoming creative blocks, urging safety professionals to rethink their approach to problem-solving. His message was clear: by embracing constraints and viewing challenges as opportunities, organizations can achieve better safety outcomes. Known for his unconventional and thought-provoking ideas, Scheele encouraged attendees to apply these insights to enhance creativity and innovation in their own safety practices.
NEWS
Your Virtual Water Cooler
SHARE THE NEWS
Enjoying the newsletter? Share it and earn some free Safety Knight swag. The more referrals you have the more you earn!
All you need is one to start earning.
