- Safety Knights Monday Mailer
- Posts
- Newsletter 30th Edition
Newsletter 30th Edition
Good morning! If you’re anything like us you spent last week frantically putting together your Mother’s Day gifts. We’re here to bring you up to speed on all the EHS news you might have missed!
THIS WEEK’S TIPS
This week’s safety upgrades:
Fall Prevention Guides
Avian Flu Update
New NIOSH, Global Surveys and OSHA Map Updates
PROFESSIONAL DEVELOPMENT
This Weeks Professional Development Tip
OSHA NEWS
New Regions, OSHA Shakes It Up.

The Department of Labor has announced strategic changes to the structure of its OSHA regional operations. These changes are designed to optimize resource allocation and enhance the agency's ability to adapt to various challenges effectively.
One significant alteration involves the establishment of a new OSHA regional office in Birmingham, Alabama. This office will have jurisdiction over several states, including Arkansas, Kentucky, Louisiana, Mississippi, Tennessee, and the Florida Panhandle. Its primary focus will be on addressing the needs of the growing worker population in these areas and overseeing industries such as food processing, construction, heavy manufacturing, and chemical processing, which are known for their hazardous work environments.
Furthermore, OSHA plans to consolidate Regions 9 and 10 into a new San Francisco Region. This move aims to streamline operations and reduce operating costs, allowing the agency to allocate resources more efficiently.
As part of the restructuring efforts, OSHA will also rename its regions to reflect their geographical locations, moving away from the current numerical designation system. For example, the region currently known as Region 4 will be renamed the Atlanta Region, with jurisdiction over Florida (excluding the Panhandle), Georgia, North Carolina, and South Carolina. Similarly, Region 6 will become the Dallas Region, overseeing workplace safety issues in New Mexico, Oklahoma, and Texas.
The restructuring plan will keep the composition of OSHA's other regions unchanged, with regions being renamed as follows:
Region 1: Boston Region
Region 2: New York City Region
Region 3: Philadelphia Region
Region 4: Atlanta Region
Region 5: Chicago Region
Region 6: Dallas Region
Region 7: Kansas City Region
Region 8: Colorado Region
Regions 9 and 10: San Francisco Region
Assistant Secretary for Occupational Safety and Health Doug Parker explained that these changes align with the nation's demographic and industrial shifts since the passage of the OSH Act. The restructuring aims to enable OSHA professionals to better serve all workers, including historically underserved populations. With a stronger enforcement presence in the South and more consolidated oversight in the West, where many states operate their OSHA programs, the agency can direct its resources more effectively.
OSHA plans to fully transition to the new regional structure later in fiscal year 2024. Once implemented, updated regional maps and contact information will be made publicly available online.
RESEARCH
New Data and Research

The ERM 2024 Global Health and Safety Survey highlights the evolving landscape of health and safety in organizations, with increased expectations and risks amid rapid workforce and workplace changes. Key findings include:
Changing Expectations: 94% of respondents noted increased stakeholder expectations over the past 3 years, with 80% expecting further rises.
Challenges in Keeping Pace: Only 2% of respondents believe health and safety professionals are fully equipped to meet evolving stakeholder needs.
Risk Factors: Managing increased use of contractors and addressing psychosocial risk factors, including mental health challenges, are growing concerns.
Investments in Health and Safety: Companies have increased health and safety investments by 26% on average over the past 3 years, with an anticipated 20% increase in the next 3 years. New technologies, particularly data analytics and automation, are prioritized.
Leadership Engagement: While 81% reported higher leadership engagement, only 7% feel leaders spend sufficient time on health and safety.
The survey underscores the need for meaningful reflection and proactive leadership to address rising expectations and challenges in health and safety management amidst ongoing workplace transformations.
Link to the full report can be found here.
National Safety Council, New Research on Location Geofencing
The National Safety Council's (NSC) Work to Zero initiative aims to combat workplace fatalities by leveraging technology. Their latest white paper, "Advancing Workplace Safety with Location Geofencing," delves into the potential of this technology to reduce serious incidents and fatalities (SIFs) in various industries.
Location geofencing, when integrated with existing safety systems, creates virtual boundaries around work areas. It enables real-time monitoring and alerts when workers enter or exit these zones. The white paper highlights the benefits, such as risk mitigation, enhanced worksite visibility, and improved efficiency through automation of safety processes.
Despite its promise, there are hurdles to widespread adoption. Privacy concerns, initial capital investments, and technological limitations may deter some employers. However, the NSC's initiative offers guidance on assessing risks and implementing safety measures effectively.
To delve deeper into this topic, you can visit nsc.org/worktozero. Additionally, you can register here for the "Addressing Workplace Safety with Location Geofencing" webinar scheduled for May 29, 2024.
PRESENTED BY RED ALERT WAX
No one will read this. Prove us wrong.

This past week was National Stand Down Week. Just because it’s over it doesn’t mean you shouldn’t do your part to tackle the #1 workplace safety problem. Red Alert Wax is designed to prevent falls from wet floors instantly.
Let’s face it, people don’t read the yellow signs, but people do anything to keep their shoes from getting wet.
FALL PREVENTION
National Stand Down Week
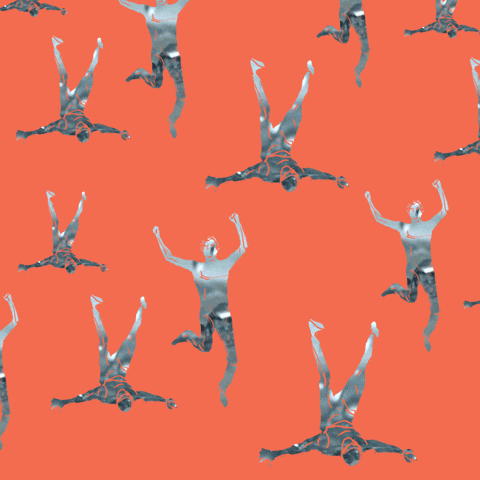
Falls from elevation ranked nationally as the second leading cause of unintentional injury-related deaths among workers. In 2022, falls accounted for 700 construction worker fatalities, according to the U.S. Bureau of Labor Statistics. To address this, the 11th annual National Safety Stand-Down to Prevent Falls in Construction was held from May 6-10, 2024. Led by OSHA, this initiative aimed to promote fall prevention practices in the construction industry.
During the 2024 National Safety Stand-Down, OSHA encouraged employers to dedicate time for discussions on fall protection and safety measures when working at heights. A safety stand-down involved temporarily halting construction activities to engage in conversations about identifying hazards, implementing preventive measures, and reinforcing safety protocols.
To support that year's Stand-Down, the Kentucky Occupational Safety and Health Surveillance (KOSHS) program released a Hazard Alert highlighting the increasing risks associated with ladder-related accidents. Rebecca Honaker, KOSHS research director, expressed concern about the rising number of ladder-related falls in Kentucky, with 447 construction worker injuries and eight fatalities between 2013 and 2022.
Ladder Safety Guide (Source):
Work above 6 feet – employ conventional fall protection, have a spotter and stage materials & equipment more than 6 feet from the edge.
Be sure straight ladders extend at least 36 inches above top support point.
Set ladders on solid footing and place base away from wall of edge approximately one foot for every four feet of vertical height.
Refrain from using ladders as a platform.
Always use three points of contact when climbing and descending.
Adjust ladder position to avoid leaning out to the side.
Key Factors in Construction Falls & Steps to Address Them (Source):
1. Make Time for Safety:
Small construction companies are especially vulnerable to fatal falls due to resource constraints and tight schedules.
Allocate sufficient time and resources for safety measures, including regular training sessions and toolbox talks.
Participate in initiatives like the National Safety Stand-Down to Prevent Falls in Construction to reinforce safety awareness and practices.
2. Ensure Proper PPE Usage:
Workers must wear fall protection equipment as required by their employer.
Enforce the use of fall protection gear through training and clear expectations from leadership.
Regularly assess the safety climate at job sites to ensure alignment between policies and practices.
3. Focus on Leading Edges:
Implement OSHA's requirements for protecting workers at leading edges, especially those 6 feet or higher above a lower level.
Conduct thorough safety evaluations and identify potential hazards, including exposed edges.
Utilize appropriate fall protection systems and lifelines to prevent accidents.
4. Emphasize Pre-Work Task Planning:
Complete pre-work task plans to identify potential hazards and obstacles.
Adapt and reprioritize efforts based on changing conditions on the job site.
Utilize resources like StopConstructionFalls.com for fall prevention plans and checklists.
5. Engineer Out Hazards:
Employ Prevention through Design (PtD) principles to mitigate risks during the design phase.
Focus on eliminating or substituting hazards at the top of the Hierarchy of Controls.
Implement engineering solutions such as embedded safety features and prefabricated structures to prevent falls.
FOOD FOR THOUGHT
New Idea Around Compliance?

Daiquiri Steele, from the University of Alabama School of Law, argues for a new approach to enforcing worker-protection statutes in response to growing concerns about employer retaliation and the limitations of the current system. Steele's proposal emphasizes proactive compliance checks over the reliance on ad-hoc enforcement triggered by individual complaints.
Currently, federal agencies enforce workplace regulations mainly through two avenues: compliance audits and individual complaint actions. Steele points out that while some agencies have a more balanced approach, occupational agencies like OSHA primarily respond to individual complaints.
Steele highlights several shortcomings of the current system, including its vulnerability to employer retaliation, its limited effectiveness in preventing future non-compliance, and its costly nature. She suggests that employee fear of retaliation reduces the number of complaints to federal agencies, leading to underenforcement of occupational safety and anti-discrimination laws.
Moreover, Steele argues that recent court decisions have further restricted the ability to make retaliation claims, making the current system even less effective. She proposes shifting the focus towards proactive compliance reviews, which would mitigate the problems posed by employer retaliation.
Under Steele's proposal, agencies would increase mandatory employer reporting of compliance activities and conduct studies on employer non-compliance. This information would then inform targeted compliance audits, allowing agencies to concentrate resources on the most problematic industries and companies.
Steele contends that her proposed system would not require additional resources and could be implemented within the existing legal framework. She suggests that agencies like the EEOC and OSHA already have the authority to adopt an audit-centric approach to enforcement.
In conclusion, Steele argues that her proposal offers a pragmatic solution to protect workers' rights in the face of growing employer retaliation, pending significant legislative or judicial reforms. What do you think?
ERGONOMICS
Bend Don’t Break.
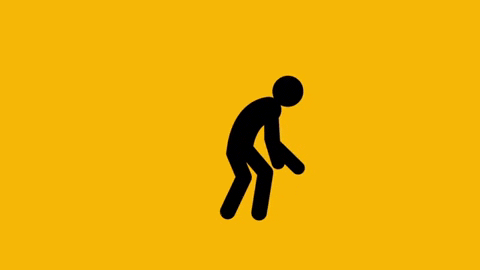
A recent study by the National Institute of Occupational Safety and Health (NIOSH) highlights the need for ergonomic safety standards in logistics facilities. At a Georgia facility, concerns over musculoskeletal disorders prompted a health hazard evaluation, revealing issues with workstations and employee discomfort, particularly in the back and shoulders.
Key Findings and Recommendations:
Workstations lacked ergonomic design to prevent musculoskeletal disorders.
Recommendations are based on a hierarchy of controls approach, focusing on hazard reduction.
Suggestions include optimizing conveyor heights, reorganizing stock, and providing anti-fatigue mats.
Regular employee input and encouragement to report health concerns are essential for improving workplace conditions.
Risk Reduction:
Design adjustments, such as optimizing conveyor heights, are crucial for preventing musculoskeletal disorders.
Reorganizing stock and providing equipment like anti-fatigue mats can further reduce ergonomic risks.
Input and Encouragement:
Establishing committees for employee input and encouraging health concern reporting can enhance safety culture.
Early recognition of symptoms and addressing workplace issues promptly can mitigate injury severity.
Conclusion:
NIOSH's study emphasizes the importance of ergonomic design and proactive measures in reducing musculoskeletal disorders in logistics facilities. By implementing ergonomic recommendations and fostering a culture of safety, employers can improve workplace conditions and prevent work-related injuries.
DON’T FORGET YOU DISCOUNT
Don’t forget your discount SKsaves10
Compliance training online is the way to go because they've got the best content and customer service in the biz. With over 30K trusted clients, including government agencies and universities, their certificates are accepted on a federal level. Trust us, we've been in business since 2008.
NEWS
Your Virtual Water Cooler
OSHA "Heat Illness Alert" urges TX employers protect workers from summer-like heat
How is CT keeping milk safe from bird flu— and preparing for a potential human pandemic?
Addressing women’s health, safety issues in solar, energy storage industry
Prioritizing Emotional Balance: Strategies for Mental Health in the Workplace
Rhode Island’s Workplace Psychological Safety Act: Ensuring Safe Work Environments
SHARE THE NEWS
Enjoying the newsletter? Share it and earn some free Safety Knight swag. The more referrals you have the more you earn!
All you need is one to start earning.
