- Safety Knights Monday Mailer
- Posts
- Newsletter 31st Edition
Newsletter 31st Edition
Good morning! "Safety has to be everyone’s responsibility… Everyone needs to know that they are empowered to speak up if there’s an issue.”
— Captain Scott Kelly
THIS WEEK’S TIPS
This week’s safety upgrades:
OSHA’s Heat Illness Prevention Guide
Electrical Safety Overview
Construction: How to Build a Safety Culture
PROFESSIONAL DEVELOPMENT
This Weeks Professional Development Tip
STATES
33% of Washington Sever Violators Let Off the Hook.
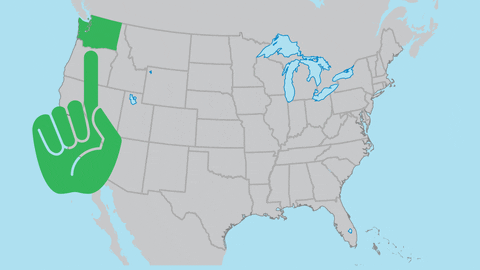
Following a trench collapse that claimed a worker's life in 2022, Washington state regulators labeled AAA Contractors a "severe violator" due to several serious safety hazards. However, over 600 days later, the state's Department of Labor & Industries (L&I) had not conducted a follow-up inspection of AAA Contractors' worksite. Similarly, Seasoft Scuba, placed on the severe violator list in 2020, had not been revisited by L&I for four years. A study by Cascade PBS found that more than a third of companies designated as severe violators in the past five years had not received re-inspections.
The Severe Violation Enforcement Program, established by L&I in 2011, aims to monitor companies with willful or repeat serious citations, with a focus on those demonstrating disregard for worker safety. Despite this, many severe violator companies, ranging from large corporations like Boeing to smaller contractors, remain on the list. While the program intends to encourage safety compliance, its effectiveness has been questioned.
Some companies on the severe violator list have contested fines and settled with L&I, often resulting in reduced penalties. For example, AAA Contractors reached a settlement with L&I in 2023, leading to a significant reduction in fines. However, some companies, like Seasoft Scuba, expressed frustration with the lack of support from L&I following their designation as severe violators.
L&I data shows that only a small percentage of companies on the severe violator list have undergone specific follow-up inspections to ensure hazards are addressed. Instead, inspections are often prompted by safety complaints or referrals, indicating a reactive rather than proactive approach to enforcement. While the program rules were updated in 2023 to impose deadlines for follow-up inspections, challenges remain in effectively monitoring and enforcing safety compliance among severe violator companies.
HEAT
No, we’re not going to stop talking about this!
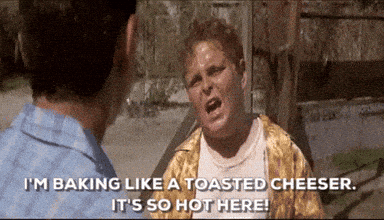
No, we’re not going to stop talking about this. Not when the numbers don’t lie and we’ve already had parts of the country issuing heat advisories for heat indexes into the triple digits….And it’s only May!
The Workers’ Compensation Research Institute's study delves into the correlation between rising temperatures and workplace injuries, particularly focusing on the impact of excessive heat on different industries and regions. Using extensive data from workers’ compensation claims spanning six years across 24 states, the study reveals a notable uptick of 5 to 6 percent in work-related accidents when temperatures surpass 90 degrees Fahrenheit. This increase is particularly pronounced in the construction sector, where injury rates surge by 14 to 20 percent during high-temperature days.
Moreover, the study highlights regional disparities, indicating a higher likelihood of heat-related injuries in the southern U.S. compared to other regions. While workers can acclimatize to some extent, especially when provided with adequate cooling measures such as air conditioning and shaded areas, the risk of workplace injuries remains significant.
Beyond immediate injury risks, the study also underscores the exacerbation of existing health conditions by excessive heat, including asthma, kidney failure, and heart disease. Furthermore, individual factors like age, medication usage, and underlying health conditions can magnify the effects of heat exposure on workplace injuries.
Despite the growing recognition of heat-related hazards, there is currently no federal occupational health and safety standard specifically addressing heat exposure. While OSHA has outlined recommendations for employers to mitigate heat-related risks, the absence of enforceable standards underscores the need for proactive measures by employers to ensure the safety and well-being of their workers.
In light of these findings, the study emphasizes the importance of implementing robust safety protocols, including adequate hydration, frequent rest breaks, provision of cool water, and access to shaded areas. Additionally, employers are urged to monitor workers closely, especially those engaged in physically demanding tasks in high-temperature environments, to prevent heat-related illnesses and injuries.
OSHA’s Heat Illness Prevention Guidelines can be found here.
PRESENTED BY REDALERT WAX
No one will read this. Prove us wrong.

Just because National Stand Down Week is over doesn’t mean you shouldn’t do your part to tackle the #1 workplace safety problem. Red Alert Wax is designed to prevent falls from wet floors instantly.
Let’s face it, people don’t read the yellow signs, but people do anything to keep their shoes from getting wet.
ELECTRICAL SAFETY
Electrical Explosion. Are You Next?
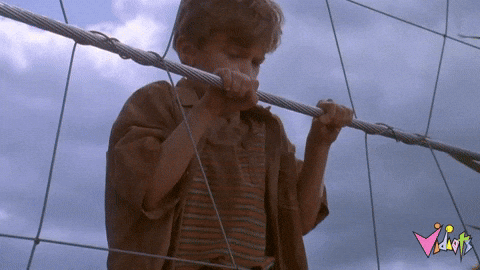
During Powerline Safety Week, the Electrical Safety Authority (ESA) emphasizes the urgent need for heightened awareness and improved training practices in the construction industry regarding overhead powerlines. Patrick Falzon, a powerline safety specialist at ESA, highlights the alarming number of incidents involving powerlines, many of which could have been prevented. Despite efforts, eight deaths occurred in the past decade alone.
A recent survey by ESA reveals a significant knowledge gap among trade workers regarding powerline safety. Only 18% correctly identified the safe distance from overhead powerlines (3 meters), and even fewer knew the safety boundary for downed powerlines (10 meters). Moreover, 70% incorrectly believed it was safe to touch a powerline if it had an orange identifier, meant for visibility, not protection.
Falzon emphasizes the importance of bridging the gap between awareness and action to ensure every worker's safety. By integrating safety training into daily operations, construction sites can mitigate the risks associated with powerlines and work towards preventing further tragedies.
Here are 6 actionable tips for a safer work environment:
Regular training sessions: Implementing routine safety training that includes specific modules on powerline safety can significantly reduce risk. Focus on interactive and engaging content to help workers retain crucial information.
Visual safety aids: Utilize clear, visible signage at job sites that illustrate safe distances and highlight the presence of powerlines. Consider using flags or other high-visibility markers instead of orange covers to avoid giving a false sense of security.
Pre-task safety briefings: Before any work begins, especially in areas where powerlines are present, conduct a safety briefing to reinforce the day's hazards and the specific precautions needed.
Promote a safety culture: Encourage workers to speak up about unsafe conditions and to actively participate in safety discussions. Recognize and reward safe behavior to reinforce its importance.
Collaborative efforts: Work with local utilities and safety authorities to provide workers with the most current information and training resources. These partnerships can also offer practical insights into the specific challenges and solutions related to powerline safety.
Access to appropriately fitting PPE: Take the time to ensure PPE is designed to work for everyone and fits appropriately. For example, women face tripping hazards, restricted movement and unsafe working conditions because of ill-fitting PPE, which puts them at risk for injury.
Electrical explosion: Worker suffers serious burns - video Dailymotion
CONSTRUCTION SAFETY
Construction Safety Culture Build.
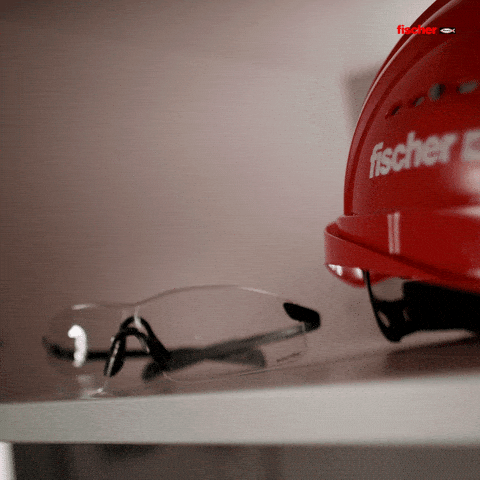
Creating a robust safety culture in the construction industry involves more than just following rules; it requires a genuine concern for everyone's well-being. Effective safety management starts with leadership commitment and engagement, empowering leaders with the right resources and skills to prioritize safety. Building trusting relationships, especially during onboarding, lays the groundwork for a thriving safety culture.
A successful safety culture goes beyond enforcement, emphasizing employee involvement and positive recognition. Personal motivations for working safely, like family, should be integrated into daily work practices. Initiatives like daily "Safety Spotlights" encourage employees to share safety concerns and volunteer for safety responsibilities. Establishing a safety committee and recognizing positive behavior further engage employees and contribute to a strong safety culture.
To protect workers, construction companies must invest in ongoing education and the safest equipment. The National Safety Council offers valuable resources for facilitating conversations about safety, complemented by data assessments to identify areas for improvement. Despite the challenges posed by the pandemic, maintaining hygiene practices and prioritizing safety are essential for sustaining a strong safety culture.
A successful safety culture attracts talent, holds everyone accountable, emphasizes prevention, promotes communication and relationships, encourages care for others, and empowers employees to follow safety procedures willingly. Through leadership commitment and ongoing efforts, construction companies can create safer work environments for everyone involved.
PSYCHOLOGICAL SAFETY
Psychologically Unsafe, or an Excuse?
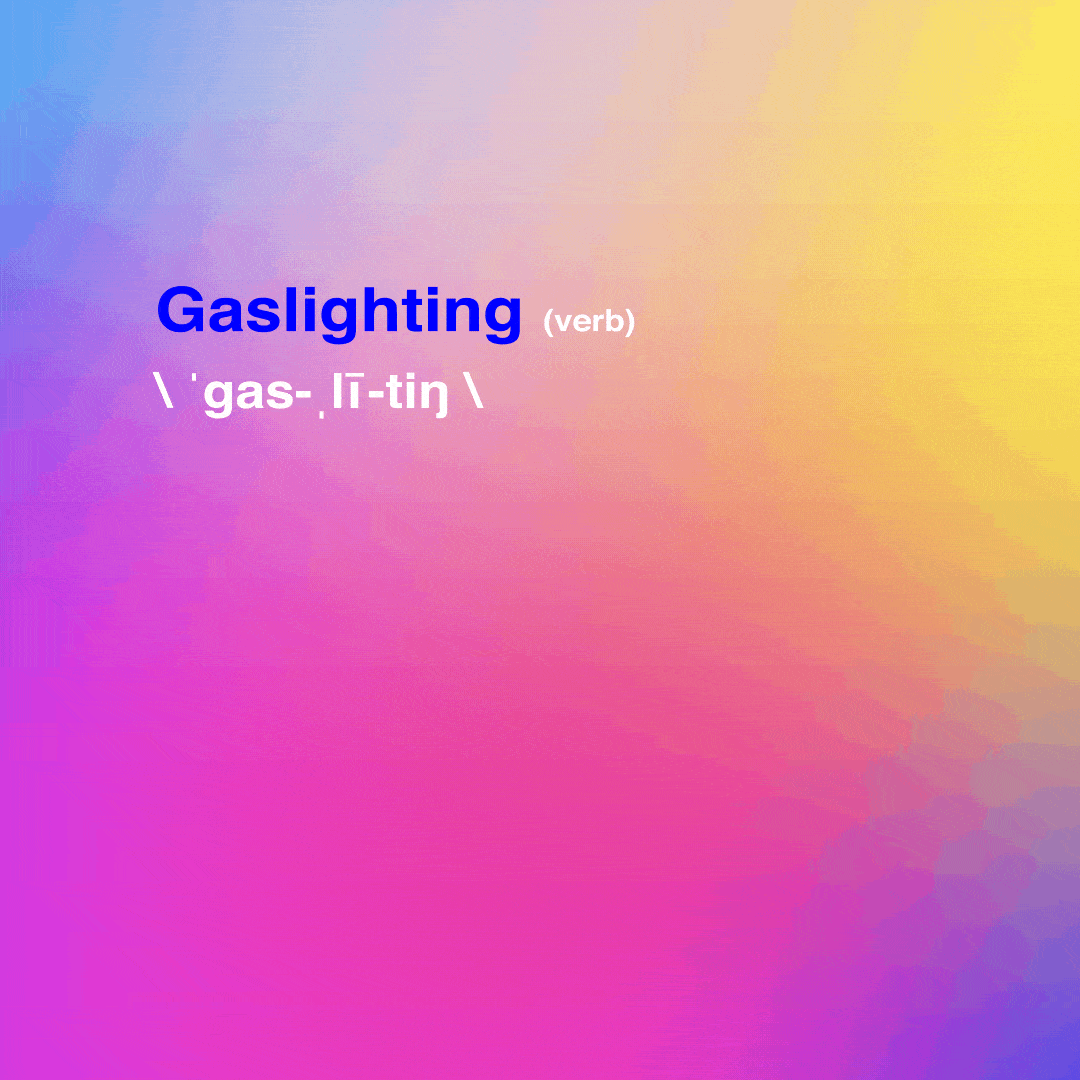
Employers are increasingly recognizing the importance of psychological safety and inclusion in the workplace, aiming to create environments where employees feel safe to speak up, share ideas, and take risks without fear of punishment or humiliation. However, there's a growing concern that some employees may misuse these concepts as a shield to avoid accountability for their actions.
When employees raise concerns about their psychological safety, leaders should listen empathetically but also focus on the behaviors at hand. Instead of immediately accepting blame-shifting statements like "I don’t feel psychologically safe," leaders should inquire further to understand the specific behaviors involved. This approach helps maintain a balance between supporting employees' well-being and holding them accountable for their actions.
It's essential for organizations to establish clear guidelines for accountability, expectations, and behaviors. Leaders should regularly communicate these expectations to ensure employees understand their roles and how they will be held accountable. Additionally, setting clear consequences for making false allegations can help deter misuse of psychological safety as an excuse to avoid responsibility.
Training leaders to become trusted figures who can navigate complex workplace dynamics is crucial. Trusted leaders can build safe and supportive relationships with employees while also addressing issues of accountability effectively.
When addressing concerns, leaders should prioritize facts over emotions. While acknowledging and validating employees' feelings is important, decisions should be based on objective evidence and behavioral observations rather than subjective emotions.
Overall, creating a psychologically safe and inclusive workplace requires a multifaceted approach that balances support for employees' well-being with a commitment to accountability and performance excellence. By promoting a culture of transparency, open communication, and mutual respect, organizations can mitigate the risk of psychological safety being misused and foster a positive work environment for all employees.
DON’T FORGET YOU DISCOUNT
Don’t forget your discount SKsaves10
Compliance training online is the way to go because they've got the best content and customer service in the biz. With over 30K trusted clients, including government agencies and universities, their certificates are accepted on a federal level. Trust us, we've been in business since 2008.
NEWS
Your Virtual Water Cooler
[Podcast] A Decade of Safety Achievement: Ten Years Without Incidents
ASSP Report Reveals Recommended Strategies to Improve Workplace Safety
Grant MS teachers call out for better workplace safety, mental health support
Safe spaces: Community members come together for safety education
CDC releases burnout prevention guidelines for healthcare workers
SHARE THE NEWS
Enjoying the newsletter? Share it and earn some free Safety Knight swag. The more referrals you have the more you earn!
All you need is one to start earning.
