- Safety Knights Monday Mailer
- Posts
- 5th Edition Monday Morning Newsletter
5th Edition Monday Morning Newsletter

Good morning! We hope you’re ready for another edition of our Monday morning newsletter! We've got the lowdown on last week’s EPA news and how it could impact your company. Plus, we've got some super cool safety tips and tricks to keep everyone safe. So if you’re ready, grab your favorite morning drink and let's dive in!
THIS WEEK’S TIPS
Tips you’ll find in this weeks edition:
Industrial Machine Safety
EPA Reporting Guidance
Fall Protection
ENVIORNMENTAL HYGIENE
Going to work? Maybe hold your breath.
Your work air is deadlier than you think.
We all know the hills of Appalachia are full of coal mines, moonshine and folk music but they are also full of something more sinister. Over the past decade, three clinics in southwestern Virginia and eastern Kentucky collectively reported over 1,500 cases of black lung disease. Also known as coal workers' pneumoconiosis (CWP), black lung disease is a lung condition caused by prolonged exposure to silica dust in coal mines, leading to inflammation, scarring, and the formation of nodules in the lungs, impairing respiratory function and death. In 2018, NPR and PBS’s Frontline documented the result of silica exposure and it’s results on one former coal miner from eastern Kentucky.
For decades, concerns about silica's contribution to black lung have been on the rise. Since 1974, mine safety advocates have been urging regulators to take action. Finally, this summer, the Mine Safety and Health Administration (MSHA) introduced a proposed regulation to limit miners' exposure to silica dust. The proposed rule change aims to double the current silica dust exposure limit, establishing a framework for direct regulation of excessive silica exposures—an unprecedented move that allows for citations and fines for endangering miners. Advocates for mine safety applaud the new exposure limit of 50 micrograms of silica per cubic meter of dust, a goal they have pursued for decades. However, if the rule is implemented, the agency projects a modest impact, saving 63 coal miner lives and preventing 244 cases of black lung disease over a span of 60 years. However believe the proposed changes don’t do enough. Since 2010, there have been 4,000 instances of complicated black lung, with over 1,500 diagnoses occurring in the past five years alone.
Mine safety advocates applaud the federal Mine Safety and Health Administration's (MSHA) proposal to double the silica dust exposure limit and directly regulate silica dust for the first time. However, concerns arise regarding the proposal's perceived leniency in allowing self-policing by mining companies, potentially undermining agency oversight and enforcement. Advocates emphasize several key issues:
Sampling Oversight: Advocates highlight the proposal's reliance on mining companies for silica dust sampling and corrective actions, calling for enhanced oversight due to a history of dust sampling fraud.
Analysis Speed: Critics argue that the current silica dust sample analysis is too slow, advocating for the adoption of quicker technology to enable immediate responses to excessive dust levels.
Work in Dangerous Conditions: The proposal permits temporary work in hazardous dust conditions, with miners using protective gear. Advocates argue for a prohibition on work until the mine atmosphere is cleared, aligning with the hierarchy of controls for workplace safety.
Expansion to All Mines: The rule extends to metal/nonmetal mines, posing a regulatory challenge. Some express concern that this inclusion may hinder protection for coal miners, while others stress the importance of safeguarding all miners.
Despite the proposal's potential improvements, advocates stress the need for robust enforcement and greater incentives for companies to comply, emphasizing the urgency of prioritizing miners' safety and health.
Breast Cancer
Air pollution, often associated with respiratory issues, has been linked to an increased risk of developing breast cancer, according to a study by the National Institute of Health. The research found that women in areas with high levels of fine particulate matter (PM2.5) were more likely to suffer from breast cancer. An increase of only 10 micrograms per cubic meter of PM2.5 was associated with a statistically significant rise in overall breast cancer incidence. Another study by French scientists found a statistically significant association between long-term exposure to fine particle air pollution, both at home and at work, and the increase risk of breast cancer.
French researchers at the European Society for Medical Oncology (ESMO) conducted an additional study, revealing that women face risks not only in their residential areas but also in their workplaces due to air quality. According to Professor Béatrice Fervers, Head of the Prevention Cancer Environment Department at Léon Bérard Comprehensive Cancer Centre, France,
“[O]ur data showed a statistically significant association between long-term exposure to fine particle air pollution, at home and at work, and risk of breast cancer. This contrasts with previous research which looked only at fine particle exposure where women were living, and showed small or no effects on breast cancer risk.”
PRESENTED BY ACCESS SAFETY SPECIALISTS
#savingyourASS.
For the past 2 weeks we have talked about workplace falls taking the top spot on OSHA Top 10 most cited workplace problems. So this week we thought we might help you #saveyourASS with Access Safety Specialists.
Access Safety Specialists takes falls seriously because they understand the devastating consequences that can occur. They are dedicated to saving your ASS, and by that, they mean your safety at work. From start to finish, they handle everything related to fall protection and confined spaces. Whether it's designing, engineering, installing, training, or inspecting, they've got your back. Don't risk your life or the lives of your friends, let Access Safety Specialists save your ASS and ensure a safe working environment at any height.

INDUSTRIAL SAFETY
3M has a serious problem.

Your top industrial safety tips you can’t miss.
In February 2022, a tragic incident unfolded at a 3M plant in Minnesota, resulting in the death of a 63-year-old worker entangled with a machine. Following the incident 3M opened an investigation and assessed it’s equipment at their U.S. and Canadian plants. The findings identified hazards linked to powered rollers. In May 2023, another unfortunate event occurred at a 3M plant in Wisconsin, claiming a worker's life during the setup of a plastic extrusion line. OSHA's investigation unveiled violations of lockout/tagout regulations during machine setup, coupled with workers circumventing machine guards. This involved cutting and removing fibers from rotating powered rollers and clearing fibers from the floor, exposing them to potential caught-in hazards. 3M now faces proposed penalties of $312,518 for two willful safety violations. 3M has since released the following statement:
"The safety and health of all our employees is our top priority, and we are deeply saddened by this tragic incident. Over the last six months, we have worked closely with federal workplace safety and health regulators in connection with their inspection of our Prairie du Chien worksite. In addition, 3M has continued to implement improvements and investments to help prevent similar incidents in the future and communicated these improvements to our employees at the worksite.
"We are currently in the process of evaluating the Occupational Safety Health Administration's Citation and Notification of Penalty, and we will continue to work with the Department of Labor to address this matter."
Industrial Machinery: 10 Essential Safety Tips
Maintaining safety in industrial machinery operations is crucial for various reasons, including worker well-being, legal compliance, and operational continuity. To ensure machinery safety, consider the following comprehensive tips courtesy of Tycoonstory:
1. Employee Training and Education:
Implement thorough training programs covering machinery operation, safety procedures, and emergency protocols.
Regularly update training to incorporate the latest safety standards and best practices.
2. Regular Maintenance and Inspection:
Conduct scheduled maintenance and inspections to identify and address issues before accidents or breakdowns occur.
Inspect all industrial parts regularly and replace worn or damaged components promptly.
3. Lockout/Tagout Procedures:
Develop and implement clear lockout/tagout (LOTO) procedures for each machine.
Ensure all workers are trained in LOTO practices and have access to functioning lockout and tagout devices.
4. Personal Protective Equipment (PPE):
Mandate the use of appropriate PPE, such as helmets, gloves, safety goggles, and ear protection.
Conduct regular assessments to ensure proper PPE usage and provide training on maintenance.
5. Machine Guarding:
Regularly inspect and maintain machine guarding to prevent access to hazardous areas.
Ensure correct installation and functionality of guards, including interlocks to shut down machinery when guards are opened.
6. Safety Signage and Labels:
Clearly label equipment with safety instructions, warnings, and operational guidelines.
Ensure legible, well-maintained signage placed prominently on machinery and in work areas.
7. Emergency Response Plans:
Develop comprehensive emergency response plans covering accident reporting, evacuations, and first aid.
Conduct regular drills and maintain well-equipped first-aid stations with trained personnel.
8. Safety Training Documentation:
Keep detailed records of safety training, inspections, and maintenance activities.
Use documentation to demonstrate compliance and identify areas for improvement.
9. Hazard Analysis and Risk Assessment:
Conduct thorough hazard analysis and risk assessments for each machine.
Involve employees in identifying hazards and regularly review and update risk assessments.
10. Continuous Improvement:
Encourage employees to report safety concerns, near misses, and hazards.
Establish a feedback mechanism for ongoing improvement, regularly reviewing and updating safety procedures.
By prioritizing these tips, you can enhance industrial machinery safety, ensuring worker protection, legal compliance, and operational stability. Remember, safety is an ongoing commitment that requires continuous training, communication, and vigilance.
ENVIORNMENTAL REGULATIONS
Your EPA Double Dip.
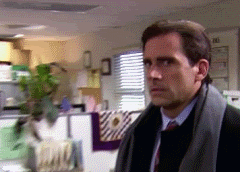
Say what?
Get ready, for two new rules if you manufacture PFAS. The EPA finalized their reporting rule regarding PFAS. One rule falls under the Toxic Substances Control Act (TSCA), and one under the Emergency Planning and Community Right to Know Act (EPCRA). According to the finalized TSCA rule anyone who has manufactured or imported PFAS “for commercial purposes” since January 1, 2011 through the end of 2022 is now required to report information on those chemicals. An article from The National Law Review explains why this is a big deal,
“These rulemakings are significant because they place broad recordkeeping and reporting requirements on facilities that may not have previous experience with either environmental statute. Under the new TSCA rule, any entity that manufactures or has manufactured (including import or previously imported) PFAS or PFAS-containing articles in any year since January 1, 2011, must now report certain information to EPA.”
As for the EPCRA rule:
“…under the new EPCRA rule, facilities that use more than 100 pounds of PFAS annually must comply with Toxics Release Inventory (“TRI”) reporting obligations and provide downstream businesses with notifications that products may contain PFAS.”
Deadlines To Know
When it comes to the TSCA rule, Dentons law firm says, important deadlines for manufactures to submit all relevant information are 18 months (or 24 months if classified as a small manufacturer). So mark your calendars for:
May 8, 2025
November 10, 2025 (for small manufacturers under the rule).
“Manufacturers subject to this rule must submit all relevant information to EPA within 18 months (or 24 months if classified as a small manufacturer) after the rule’s effective date, which is November 13, 2023. Therefore, as it currently stands, the two relevant dates to track for reporting purposes are May 8, 2025 and November 10, 2025 (for small manufacturers under the rule). To comply with the reporting deadlines, manufacturers should first determine whether the rule applies to them, and—if so—begin taking steps to comply with the rule.”
For the EPCRA rule:
Scheduled to go into effect November 30, 2023 with a January 1, 2024 annual report start date.
What To Do?
If you think your company could be affected by this rule, it's advisable to promptly create a plan to assess whether your company has produced or imported PFAS since January 1, 2011. Furthermore, if your company has acquired another business since January 1, 2011, we suggest examining the acquired company's records to identify any potential additional reporting obligations.

Gif by theoffice on Giphy
Summary
EPA PFAS Rules Overview:
Two rulemakings finalized in October 2023: TSCA and EPCRA.
Focus on per- and polyfluoroalkyl substances (PFAS), known as "forever chemicals."
TSCA Rule Details:
Requires reporting on PFAS uses, production volumes, byproducts, disposal, exposures, and health effects.
Entities manufacturing or importing PFAS since January 1, 2011, must report through EPA's Chemical Data Exchange portal.
Reporting deadlines vary based on entity size and PFAS usage history.
EPCRA Rule Highlights:
Revised Toxics Release Inventory (TRI) program for 189 specified PFAS.
Annual reporting obligation for facilities using over 100 pounds of PFAS.
Business-to-business downstream notifications required for PFAS presence in products.
Removal of de minimis exception for PFAS content triggers reporting and notification obligations.
Overall Impact and Recommendations:
Likely impact on electronics, food packaging, automotive, textiles, circuit boards, wires, cables, and pharmaceutical industries.
Companies advised to determine PFAS manufacturing or import history since January 1, 2011.
Acquired companies' documentation should be reviewed for additional reporting requirements.
Awareness and strategies needed for TRI reporting and downstream notifications.
Conclusion:
Complex rulemakings with significant impacts on industrial and manufacturing industries.
Anticipated to be the beginning of PFAS regulatory developments.
DON’T FORGET YOU DISCOUNT
Don’t forget your discount SKsaves10
Compliance training online is the way to go because they've got the best content and customer service in the biz. With over 30K trusted clients, including government agencies and universities, their certificates are accepted on a federal level. Trust us, we've been in business since 2008.
NEWS
Your Virtual Water Cooler
In a surprising twist, Dutch Inspectors stumbled upon gas masks with asbestos filters aboard a bulk carrier during a routine inspection.
Prepare to cringe as employees unveil the 80 most unreal workplace disasters through shocking snapshots.
In a bid to clean up the mess, a legislative fix is on the horizon after a brave worker blew the whistle on Water Gremlin.
The NLRB and OSHA have joined forces to strengthen their legal enforcement efforts, creating a powerful alliance for workers' rights.
SHARE THE NEWS
Enjoying the newsletter? Share it and earn some free Safety Knight swag. The more referrals you have the more you earn!
All you need is one to start earning.
