- Safety Knights Monday Mailer
- Posts
- Newsletter 39th Edition
Newsletter 39th Edition
THIS WEEK’S TIPS
This week’s safety upgrades:
$12.7 million in training grants
Mold Prevention
Olympic Mental Health Upgrades
PROFESSIONAL DEVELOPMENT
This Weeks Professional Development Tip
OSHA
Slap in the face to every worker.
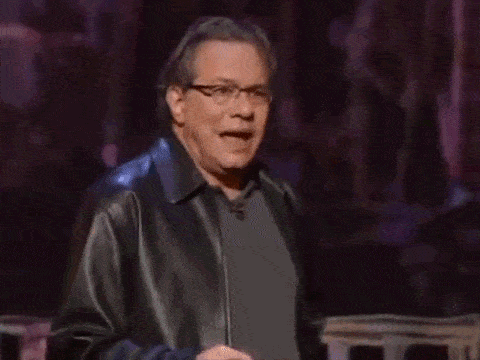
Ladies and gentlemen, gather 'round and buckle up, because what you're about to hear is nothing short of infuriating. We're diving into the seething abyss of corporate negligence, where the sheer audacity and callous disregard for human life would make even the most jaded among us want to scream. Picture this: in the grand, grotesque theater of workplace safety, we have companies so brazenly irresponsible, so contemptuously indifferent, that it's enough to make your blood boil and your head spin. This isn't just a failure of basic decency—it's a slap in the face to every worker who gets up in the morning, hoping to come back home in one piece. So, hold onto your sanity, because we're about to dissect the jaw-dropping atrocities committed by Quala Services and Boston Waterproofing & Construction Corp. Get ready to rage.
Boston Waterproofing & Construction Corp. faced severe penalties from the U.S. Department of Labor’s OSHA after exposing workers to life-threatening conditions at residential sites in Arlington, MA, and Warwick, RI, within a span of three months in late 2023. OSHA found that the company's supervisor ordered untrained day laborers into unprotected excavations despite their safety concerns, leading to cave-ins at both locations that injured and buried workers. At the Arlington site, the employer failed to rescue the trapped worker and obstructed medical assistance, while at the Warwick site, the employer disregarded the injured worker's requests for emergency help and provided inadequate medical care.
OSHA cited Boston Waterproofing for willful and serious violations, including lack of cave-in protection and training, failure to inspect excavations, and neglecting to provide emergency medical services at the Warwick site. The agency proposed total penalties of $451,694 for the violations, emphasizing the employer's exploitation of day laborers in unsafe conditions. Despite opportunities to contest the citations, Boston Waterproofing did not respond, finalizing the citations in April and May 2024. OSHA urged workers to know their rights under federal safety laws and emphasized the importance of safety protocols in trenching operations to prevent accidents.
Meanwhile, a Texas tanker cleaning company, Quala Services LLC, has been cited for numerous safety violations after multiple worker fatalities. OSHA announced on July 8 that the Houston-area company faces $810,703 in penalties. Quala Services, which cleans tankers used for hazardous materials, failed to meet federal safety standards, leading to fatal incidents.
In December 2023, two days before Christmas a worker was found dead after the company neglected to perform necessary atmospheric testing inside a tank. The company received eight repeat violations from OSHA. Previously, in November 2019, two workers died in similar circumstances, and OSHA cited the company for the same violations. The infractions included failing to prevent unauthorized entry into confined spaces, not providing attendants during confined space entries, and various issues related to entry permits and emergency protocols. OSHA Area Director Larissa Ipsen said, “Had Quala Services acted responsibly and made the safety reforms as required in 2020, another employee would not have lost their life,” she went on to condemned Quala Services for their lack of safety reforms, emphasizing that compliance with safety standards is mandatory.
PRESENTED BY EHS MOMENTUM
Tired of the Bait and Switch?

EHS Momentum was created to help companies unlock the value of an operations focused EHS program and takes a personal approach to client services.
Discover the power of an integrated EHS management system, where cutting-edge technology meets expert-driven strategies designed to integrate safety and compliance into your daily operations. Modernize your approach to EHS standards and practices with a comprehensive solution that will drive employee accountability, automate program administration, and enhance your safety culture.
Looking to learn more? Book your demo today with a company that is committed to gaining clients, not customers.
HEAT PROTECTION
Has Work Finally Become the 10th Circle of Hell?
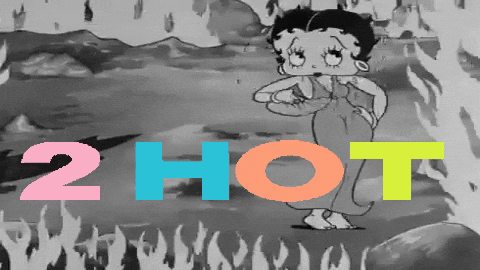
The Office of the Inspector General (OIG) released a detailed report highlighting severe safety issues at the Department of Public Works' (DPW) Cherry Hill site in Baltimore. This report came after employees filed a complaint on June 5, stating that DPW failed to provide essential resources such as water, ice, and fans, particularly for those working on routes during the summer heat.
The OIG's initial visit on June 6 confirmed these complaints. The ice machine at the site had been inoperable since summer 2023, forcing employees to purchase ice daily. The locker room lacked air conditioning or fans, exacerbating the harsh working conditions. During a follow-up visit to a recycling route on June 14, workers reported that they had not received water, ice, or Gatorade at the start of their shift, despite the temperature being 80 degrees and expected to rise to 90 degrees. Additionally, the trash truck lacked air conditioning and had mechanical issues.
Given these conditions, the OIG deemed the situation critical, especially during a Code Red alert in Baltimore, where temperatures were dangerously high. This prompted an emergency follow-up visit on June 26, during which officials observed conditions that urgently needed remedy.
The OIG found that the Cherry Hill site violated OSHA regulation 1915.88(b)(2), which mandates employers provide adequate potable drinking water for employees. Following the release of the report, DPW issued a statement acknowledging their responsibility for employee safety. They outlined various measures taken to address the issues, such as:
Equipment and Gear: Providing lightweight, breathable clothing to employees.
Training and Education: Offering comprehensive training on the risks of heat-related illnesses and the importance of preventive measures.
Cooling Resources: Ensuring work sites have ample water, shaded rest areas, and cooling stations.
Facility Upgrades: Recognizing the need for repairs, particularly at the Reedbird Sanitation Yard. DPW replaced parts of the ice machine, added an additional machine, delivered water onsite, and installed portable air conditioners. They are also planning facility upgrades, including improvements to the air conditioning system, floors, lockers, and other necessary updates.
DPW emphasized their commitment to improving working conditions and protecting their employees from the risks posed by extreme heat. This report underscores the importance of workplace safety, especially during high-temperature conditions, and the need for employers to take proactive measures to ensure the well-being of their staff.
Oregon
As a heat wave sweeps through Oregon and the Western U.S., new workplace safety regulations and increased penalties are set to be enforced by Oregon OSHA. With temperatures in the Portland metro area hovering around 100 degrees for four consecutive days and predictions of continued above-average heat, Oregon OSHA has initiated approximately 186 inspections since June 15, including about 50 since July 1, to address potential heat-related hazards. These new regulations, permanently enacted at the beginning of the year, were developed in response to a 2021 record-breaking heat wave that led to at least five worker deaths. Oregon OSHA's heat emphasis program ensures that inspectors address heat concerns during all summer inspections, not just those specific to heat, and corrections are often made during inspections before citations are issued.
The new workplace rules require all employers in Oregon to protect workers from extreme heat by providing water, shade, rest, training, and acclimatization. Specifically, when temperatures exceed 80 degrees, employers must offer shaded, ventilated, or open rest areas, provide four cups of water per worker, and ensure water is kept under 77 degrees. They must also allow breaks to prevent heat-related illness, offer training on compliance and heat dangers, and develop acclimatization plans. Additionally, protocols for medical assistance must be in place for employees working alone. Vulnerable workers, particularly those in their first week on the job, are at higher risk of heat-related illness. Oregon OSHA also provides consulting services to assist employers with health and safety compliance, helping to mitigate the risks posed by extreme heat. The link to those services can be found here.
Nevada
Despite record-breaking heat across Nevada, the state lacks enforceable regulations to protect workers from extreme temperatures, the leading cause of injury in Nevada. Heat accounted for nearly 50% of injury claims filed with Nevada OSHA from 2020 to 2024 and 30% of compensation claims. In 2023, Nevada OSHA received 392 heat-related complaints, the highest number on record. June 2024 saw the hottest temperatures recorded in Las Vegas since the 1930s, with an average of 94.6 degrees and reaching 120 degrees on July 7. This extreme heat affects not just outdoor workers but also those in high-risk industries like accommodation, food services, retail trade, and manufacturing. Recently, workers at the OYO Hotel & Casino off the Las Vegas Strip reported air conditioning problems, prompting complaints to Nevada OSHA. The casino has been using swamp cooler-type fans and portable AC units to address the issue.
Nevada OSHA relies on a "general duty clause" to address heat hazards, but labor groups argue it is insufficient. Efforts to pass specific heat regulations have been slow. A proposal requiring emergency medical services for heat illness, air conditioning repairs, and employee training was submitted in June but won't be approved until at least 2025. Previous legislative attempts to mandate water, breaks, and shade failed. For now, Nevada OSHA adopts federal guidelines without enforcement power, leaving workers vulnerable. A proposed federal rule mandating water breaks, shaded rest areas, and heat illness prevention plans offers hope but will take years to finalize. Once effective, Nevada’s plan must be as effective as the federal rule to address the state’s unique needs.
HEALTH
OSHA’s Guide, Mold in the Workplace and You.
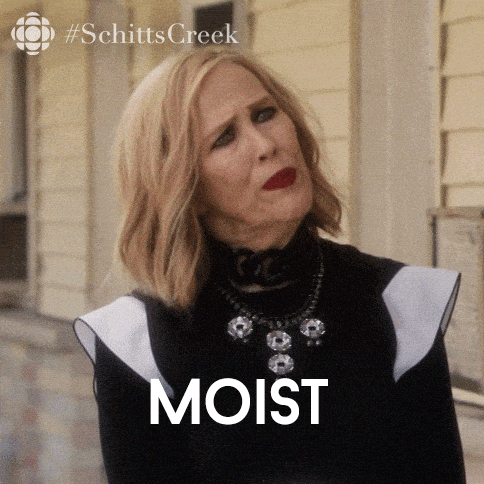
Let’s spill the chili beans!
The U.S. EPA warns that some molds can produce toxic byproducts called mycotoxins under certain conditions, especially in moisture-damaged buildings. Over 200 mycotoxins from common molds have been identified, with many more likely undiscovered. The production of mycotoxins varies based on environmental and genetic factors.
EPA notes that while some mycotoxins are known to impact human health, the effects of many remain unclear, and ongoing research is necessary. Exposure to mycotoxins can occur through inhalation, ingestion, and skin contact, and it's advisable to avoid unnecessary inhalation of mold. Elevated mold levels, with or without mycotoxins, can act as allergens, respiratory irritants, and asthma triggers, and can cause fungal infections in individuals with weakened immune systems.
OSHA says, “Moisture control is the key to mold control. When water leaks or spills occur indoors - act promptly. Any initial water infiltration should be stopped and cleaned promptly. A prompt response (within 24-48 hours) and thorough clean- up, drying, and/or removal of water-damaged materials will prevent or limit mold growth.”
Mold prevention tips include:
Repairing plumbing leaks and leaks in the building structure as soon as possible.
Looking for condensation and wet spots. Fix source(s) of moisture incursion problem(s) as soon as possible.
Preventing moisture from condensing by increasing surface temperature or reducing the moisture level in the air (humidity). To increase surface temperature, insulate or increase air circulation. To reduce the moisture level in the air, repair leaks, increase ventilation (if outside air is cold and dry), or dehumidify (if outdoor air is warm and humid).
Keeping HVAC drip pans clean, flowing properly, and unobstructed.
Performing regularly scheduled building/ HVAC inspections and maintenance, including filter changes.
Maintaining indoor relative humidity below 70% (25 - 60%, if possible).
Venting moisture-generating appliances, such as dryers, to the outside where possible.
Venting kitchens (cooking areas) and bathrooms according to local code requirements.
Cleaning and drying wet or damp spots as soon as possible, but no more than 48 hours after discovery.
Providing adequate drainage around buildings and sloping the ground away from building foundations. Follow all local building codes.
Pinpointing areas where leaks have occurred, identifying the causes, and taking preventive action to ensure that they do not reoccur.
Questions That May Assist in Determining Whether a Mold Problem Currently Exists
Are building materials or furnishings visibly moisture damaged?
Have building materials been wet more than 48 hours?
Are there existing moisture problems in the building?
Are building occupants reporting musty or moldy odors?
Are building occupants reporting health problems that they think are related to mold in the indoor environment?
Has the building been recently remodeled or has the building use changed?
Has routine maintenance been delayed or the maintenance plan been altered?
Additional info can be found on OSHA’s Guide to Mold in the Workplace page here.
MENTAL HEALTH
Olympic Mental Health Upgrades for Work.
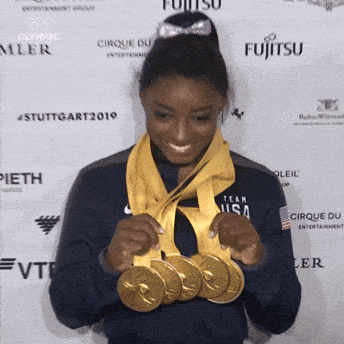
As the world eagerly anticipates the upcoming Olympics, the spotlight not only shines on the athletes' physical prowess but also on their mental health. This heightened awareness can be traced back to Simone Biles' courageous decision during the 2021 Olympics to prioritize her mental well-being by withdrawing from the competition after experiencing a "mental block." Her public act of self-care catalyzed a broader discussion on mental health, particularly within sports and workplaces, emphasizing the need for supportive environments for mental wellness.
The collective stress from the COVID-19 pandemic has significantly increased the prevalence of mental health issues. A 2023 survey by the Mental Health Association revealed a notable rise in mental illness diagnoses, with 45% of adults aged 35-44 reporting mental health issues, compared to 31% in 2019. The American Psychological Association cautions that the lingering effects of the pandemic continue to impact mental and physical health, despite a superficial return to normalcy.
As these numbers continue to rise every year, employers need to be prepared to address mental head on to ensure a healthy workforce. Recommended strategies include promoting a supportive workplace culture, integrating mental health into benefits programs, and creating clear policies for mental health support. Providing resources, training managers, routinely checking in with employees, and establishing a confidential, open-door policy are also vital steps.
In this context, the concept of psychological safety becomes crucial. Amy Gallo, a contributing editor at Harvard Business Review and workplace conflict expert, explains that psychological safety is often misunderstood. Her insights, shared on the HBR’s Women at Work podcast and in her book "Getting Along: How to Work with Anyone (Even Difficult People)," emphasize defining psychological safety, assessing its presence within teams, and strategies for cultivating it. Key elements include leadership, organizational culture, emotional intelligence, and effective team dynamics.
The integration of mental health awareness and psychological safety in workplaces is essential for fostering environments where employees can thrive both mentally and physically. As these discussions continue to evolve, they reflect a growing recognition of the interconnectedness of mental health and overall well-being.
Read more: Alarming mental health crisis among workers
DON’T FORGET YOU DISCOUNT
Don’t forget your discount SKsaves10
Compliance training online is the way to go because they've got the best content and customer service in the biz. With over 30K trusted clients, including government agencies and universities, their certificates are accepted on a federal level. Trust us, we've been in business since 2008.
NEWS
Your Virtual Water Cooler
Current COVID Uptick Appears to Be Coming With New Symptoms, Like Stomach Issues
Dollar General agrees to pay $12 million fine to settle alleged workplace safety violations
Dollar General has 48 hours to make stores safe or face more penalties after $12m workplace fine
Lead exposure concerns forces Bunnings to change product packaging
OSHA cites Jackson County Animal Shelter for workplace safety violations
Musculoskeletal injuries time-loss claims costs B.C. over $2 billion in five years
Labor Department Announces Investment in Employee Safety, Health Training, and Education ($12.7 million)
SHARE THE NEWS
Enjoying the newsletter? Share it and earn some free Safety Knight swag. The more referrals you have the more you earn!
All you need is one to start earning.
